متد دمینگ چیست؟ راهنمای جامع بهبود کیفیت و بهرهوری
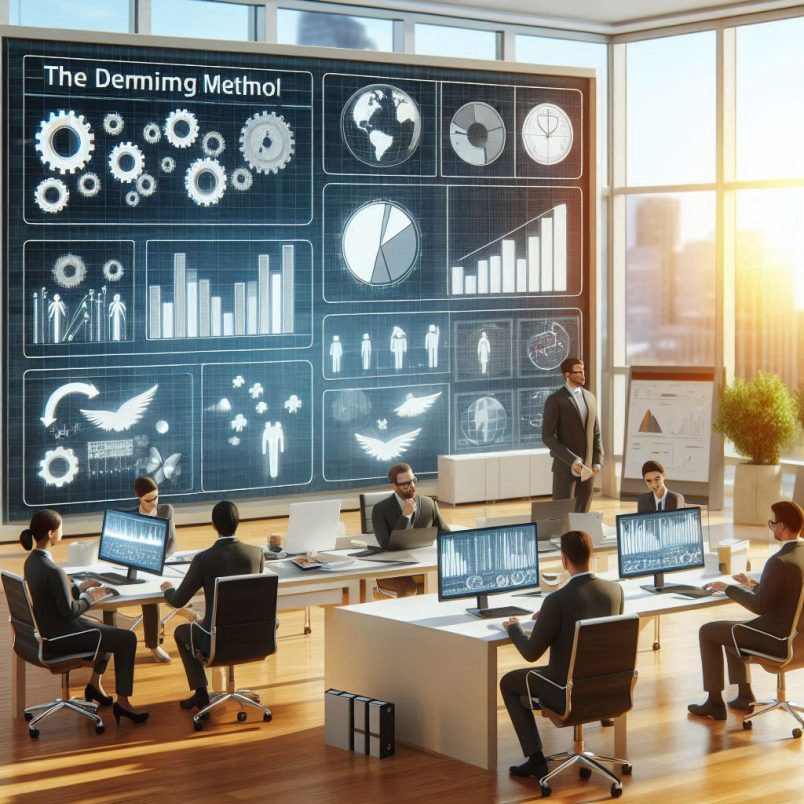
- ۱. چه کسانی از متد دمینگ استفاده میکنند؟
- ۲. پیشینه و مبانی نظری متد دمینگ
- آموزش مدیریت ۲۰۲۵ | مهارت های کلیدی برای مدیران حرفهای
- ۳. اصول و ابزارهای کلیدی متد دمینگ
- ۴. تأثیرات متد دمینگ بر کسبوکار
- ۵. چالشها و موانع اجرای متد دمینگ
- ۶. نقش و تجربه استاد محسن متمکن
- ۷. نحوه شروع پیادهسازی متد دمینگ
- ۷. مثالهای عملی از شرکتها و کشورها
- ۸. نتیجهگیری
- منابع
متد دمینگ چیست؟ راهنمای جامع و عملی برای بهبود کیفیت و بهرهوری
متد دمینگ چیست؟ این روش مدیریتی چارچوبی است بر پایهٔ کنترل آماری کیفیت (SPC) و بهبود مستمر (CI – Continuous Improvement) که توسط دکتر ویلیام ادوارد دمینگ در نیمهٔ قرن بیستم معرفی شد. در این مقاله خواهید آموخت که این متد چگونه شکل گرفت، چه اصول و ابزارهایی دارد، چه کسانی از آن استفاده میکنند، مزایا و چالشهایش چیست و چگونه استاد محسن متمکن آن را در کسبوکارهای ایرانی پیادهسازی میکند.
۱. چه کسانی از متد دمینگ استفاده میکنند؟
- اعضای هیاتمدیره شرکتهابرای تدوین استراتژی کیفیت و پایش عملکرد بلندمدت، دمینگ چارچوبی نظاممند برای تصمیمگیری دادهمحور فراهم میکند.
- مدیران و مالکین کسبوکارهاجهت بهینهسازی فرآیندها، کاهش ضایعات و ارتقای ارزیابی عملکرد تیمها و واحدها.
- کارآفرینان و افراد قصد راهاندازی کسبوکاربرای پیادهسازی شیوههای کنترل کیفیت از ابتدا، به ویژه در صنایع تولیدی و خدماتی.
- سرمایهگذارانبرای سنجش پایداری عملیات، اثربخشی مدیریت عملکرد و ریسکهای عملیاتی قبل از سرمایهگذاری.
- دانشجویان و فارغالتحصیلان مدیریت و مهندسیبرای درک علمی ابزارهای TQM، SPC و روشهای بهبود مستمر و کاربرد آنها در پروژهها.
- مالکین و علاقهمندان به استارتآپبه منظور به کارگیری متدهای Lean و Agile و تطبیق سریع با بازخورد بازار.
- مدیران عالی شرکتهای متوسط و بزرگبرای یکپارچهسازی استانداردهای سازمانی، گزارشدهی دقیق به هیاتمدیره و بهبود فرهنگ کیفیت.
۲. پیشینه و مبانی نظری متد دمینگ
۲.۱. زندگی و فعالیتهای دکتر ویلیام ادوارد دمینگ
دکتر دمینگ (1900–1993)، مهندس آماری آمریکایی و استاد دانشگاه ییل و کلمبیا، علاقهمند به کاربرد آمار در صنعت بود. در دههٔ ۱۹۴۰، او تحت تأثیر تئوریهای والتر شوارتز قرار گرفت که نمودارهای کنترل را توسعه داده بود. دمینگ این ایدهها را در صنایع آمریکا اعمال کرد اما بهدلیل تمرکز صنعت آمریکا بر کمیت تولید و هزینهٔ کم، استقبال کمی از روشهای او شد. پس از جنگ جهانی دوم، سازمانهای ژاپنی به دنبال بازسازی صنعتی بودند و از این رو از تخصص دمینگ بهره بردند.
۲.۲. همکاری با ژاپن و «معجزه اقتصادی»
در سال 1950، دولت ایالات متحده دکتر دمینگ را دعوت کرد تا به بازسازی صنعت ژاپن کمک کند. او با آموزش کنترل آماری کیفیت (SPC) به مدیران ژاپنی و معرفی فلسفه بهبود مستمر، نقش مهمی در افزایش کیفیت محصولات ژاپنی داشت. نتیجهٔ این تلاشها، جهش کیفی و رشد صادرات ژاپن در دههٔ ۵۰ و ۶۰ میلادی بود که به “معجزه اقتصادی ژاپن” معروف شد. در سال 1951، مؤسسهٔ ژاپنی مدیریت کیفیت (JUSE) جایزهٔ دمینگ را برای تشویق سازمانهای برتر در بهبود کیفیت
۲.۳. توسعهٔ متد دمینگ در غرب
از دههٔ ۱۹۸۰ به بعد، شرکتها در اروپا و آمریکا با افزایش رقابت جهانی و نیاز به کیفیت برتر، به متد دمینگ روی آوردند. چارچوب دمینگ بهعنوان بخشی از مدیریت کیفیت جامع (TQM) و برنامههای بهبود مستمر (CI) شناخته شد و در صنایع مختلف اعم از خودروسازی، الکترونیک، خدمات مالی و بهداشتی اجرا شد.
پیشنهاد میکنیم تعریف مدیریت را از نگاه ما بخوانید
آموزش مدیریت ۲۰۲۵ | مهارت های کلیدی برای مدیران حرفهای
۳. اصول و ابزارهای کلیدی متد دمینگ
۳.۱. حلقهٔ PDCA (چرخهٔ دمینگ)
PDCA مخفف Plan (برنامهریزی)، Do (اجرا)، Check (بررسی) و Act (اقدام) است. این چرخه بهصورت مداوم تکرار میشود:
- Plan: تعیین هدف، تحلیل وضعیت فعلی و طراحی اقدامات.
- Do: اجرای برنامه در مقیاس کوچک یا پایلوت.
- Check: اندازهگیری نتایج و مقایسه با اهداف. استفاده از نمودارهای کنترل (SPC).
- Act: استانداردسازی موفقیتها و اصلاح نقاط ضعف پیش از اجرای گسترده.
۳.۲. کنترل آماری فرآیند (SPC)
- نمودار کنترل X̄ و R: پایش میانگین و دامنهٔ تغییرات یک فرآیند.
- قائهٔ طبیعی و تغییرات: تمایز بین تغییرات عادی و غیرعادی برای جلوگیری از واکنشهای غیرضروری.
۳.۳. تحلیل ریشهٔ مشکل (Root Cause Analysis)
روش «۵ چرا» و نمودار ایشیکاوا (Fishbone) برای شناسایی علل اصلی خطاها و مشکلات استفاده میشود. این ابزار کمک میکند تا بهجای رفع علائم، با ریشهٔ مسائل مقابله کنیم.
۳.۴. مدیریت ایزو و استانداردها
متد دمینگ با استانداردهای ISO 9001 (مدیریت کیفیت) همافزایی دارد و اجرای آن به شرکتها برای دریافت گواهینامههای بینالمللی کمک میکند.
۴. تأثیرات متد دمینگ بر کسبوکار
۴.۱. کاهش هزینهها و ضایعات
مطالعات نشان میدهد بهکارگیری SPC و PDCA میتواند تا ۳۰–۵۰٪ هزینههای تولید را کاهش دهد، از طریق کاهش ضایعات، بازکاری و توقف خطوط تولید :contentReference[oaicite:1]{index=1}.
۴.۲. افزایش کیفیت و رضایت مشتری
کیفیت یکنواخت محصولات و خدمات منجر به افزایش اعتماد و وفاداری مشتریان میشود. بازخورد مستمر مشتری در چرخهٔ PDCA به تطبیق سریعتر با نیازهای بازار کمک میکند.
۴.۳. بهبود بهرهوری و انگیزه کارکنان
شفافیت در اهداف و معیارها، مشارکت کارکنان را افزایش داده و حس مسئولیتپذیری را تقویت میکند؛ در نتیجه بهرهوری سازمان بهبود مییابد.
۴.۴. تصمیمگیری مبتنی بر داده
استفاده از آمار و اطلاعات دقیق، پیشبینیپذیری را بالا برده و ریسک تصمیمات مدیریتی را کاهش میدهد.
۵. چالشها و موانع اجرای متد دمینگ
- مقاومت در برابر تغییر: فرهنگ سازمانی نیاز به پذیرش روشهای جدید دارد.
- زیرساختهای دادهای ناکافی: بدون سیستمهای اطلاعاتی قوی، گردآوری و تحلیل داده مشکلساز است.
- هزینههای اولیه: سرمایهگذاری در آموزش، نرمافزارها و مشاوره تخصصی
- نگهداری و استمرار: پروژههای مقطعی اثربخشی پایدار ندارند؛ نیاز به برنامهریزی بلندمدت است.
۶. نقش و تجربه استاد محسن متمکن
استاد محسن متمکن با بیش از ده سال تجربه مشاوره مدیریت و دورههای تخصصی در زمینهٔ مدیریت عملکرد و کنترل کیفیت، متد دمینگ را در صنایع مختلف ایران بهکار برده است ، بهتر است بدانید این متد در آکادمی متمکن با روش دانشگاه هاروارد به مدیران ارجمند و به صورت مطالعه موردی و عملی آموزش داده می شود:
- طراحی و اجرای چرخهٔ PDCA در شرکتهای متوسط و بزرگ
- برگزاری کارگاههای عملی ارزیابی عملکرد و SPC در دورههای سازمانی
- ارائه خدمات مشاوره به شرکتهای تولیدی، خدماتی و استارتآپها
- بهینهسازی سئوی محتوای داخلی با ابزار RankMath برای گزارشها و مستندات کیفیت
- مستندسازی موفقیتهای کیفی و نشر کِیساستادیهای ایرانی
۷. نحوه شروع پیادهسازی متد دمینگ
- ارزیابی وضعیت فعلی: تعیین KPIهای کیفیت و شناسایی مشکلات اصلی.
- آموزش تیم مدیریتی و کارکنان: کارگاههای SPC، PDCA و RCA.
- اجرای پروژهٔ پایلوت: انتخاب یک فرآیند کلیدی و اجرای چرخه PDCA.
- گسترش تدریجی: پس از ارزیابی موفقیت، توسعه به سایر واحدها.
- تثبیت و استانداردسازی: مستندسازی و یکپارچهسازی در نظام مدیریت کیفیت (ISO 9001).
۷. مثالهای عملی از شرکتها و کشورها
در حال حاضر، بسیاری از شرکتهای بینالمللی و سازمانهای پیشرو از متد دمینگ برای بهبود کیفیت و بهینهسازی فرآیندهای خود استفاده میکنند. در زیر ۸ شرکت برتر که مبنای مدیریتی خود را بر اساس اصول دمینگ قرار دادهاند آمده است:
- Toyota – استفاده از چرخه PDCA در تولید خودرو و سیستم تولید ناب (Lean).
- Ford – پیادهسازی کنترل آماری کیفیت در خطوط مونتاژ.
- General Electric (GE) – بهکارگیری ابزارهای Six Sigma که مبتنی بر اصول دمینگ است.
- Intel – استفاده از SPC برای تضمین کیفیت چیپهای نیمههادی.
- 3M – فرهنگ بهبود مستمر و نوآوری سیستماتیک.
- Procter & Gamble (P&G) – ارتقای مستمر در زنجیره تأمین و تولید محصولات مصرفی.
- IBM – مدیریت فرآیندهای خدماتی و پروژههای نرمافزاری با چرخههای مکرر PDCA.
- Siemens – استانداردسازی سیستمهای مدیریتی و کیفیت در صنایع سنگین و مهندسی.
علاوه بر شرکتها، این روش در بسیاری از کشورها نیز بهعنوان ابزار توسعه اقتصادی و صنعتی در حال اجراست. سه کشوری که بهطور چشمگیر دمینگ را در برنامههای ملی و صنعتی خود گسترش دادهاند عبارتند از:
- ژاپن – مبدع اجرا و ترویج متد پس از جنگ جهانی دوم.
- آلمان – ادغام اصول دمینگ در استانداردهای صنعتی ISO و صنایع خودروسازی.
- چین – استفاده از TQM و بهبود مستمر در پروژههای عظیم تولیدی و زیرساختی.
۸. نتیجهگیری
متد دمینگ با تأکید بر بهبود مستمر و تصمیمگیری مبتنی بر داده، ابزار قدرتمندی برای ارتقای کیفیت، کاهش هزینه و افزایش رضایت مشتری است.در کنار این متد روش و روی کرد متد هاروارد بیزینس اسکول می تواند معجزه ی مدیریت و عملکرد را نمایش دهد . اگر میخواهید این روش را در کسبوکار خود پیاده کنید و از تجربیات استاد محسن متمکن بهرهمند شوید، همین حالا در دورهٔ مقدماتی مهارتهای ضروری ویژه مدیران ثبتنام کنید و قدم اول در مسیر تحول سازمانی را بردارید.
منابع
- Deming, W.E. (1986). Out of the Crisis. MIT Press.
- JUSE. (1951). “Deming Prize History.”
- Oakland, J.S. (2014). Total Quality Management and Operational Excellence. Routledge.
- Lean Enterprise Institute. (2020). “Principles of Lean.”
- Harvard Business Review. (2019). “How Customer Feedback Fuels Continuous Improvement.”
برای ارسال نظر لطفا ابتدا وارد حساب کاربری خود شوید. صفحه ورود و ثبت نام